Know Your Place, Trash!
- thechlorophyllclub
- Oct 22, 2021
- 3 min read
Updated: Mar 1, 2022
Have you ever wondered what happened to that slimy banana peel you mindlessly chucked in the garbage bin? Well, since you’re reading this article, you’re either interested in the preservation of the environment or incredibly bored, so sit back and prepare to absorb this fascinating factoid.
Elif Bilgin, a 16-year-old girl from Istanbul, Turkey, won $50,000 at the Google Science Fair in 2013 for her process of turning banana peels into bio-plastic. Now, she can buy like half a Mazda for ushering in the future.
However, the true origins of this technique can be traced back to the UNSW located in Sydney, Australia. In this method, the pseudo stem of the banana plant is converted into nanocellulose and it is then used to create bioplastic. Because only 12% of the total banana plant makes up for the actual bananas and the rest of the plant is considered to be a ‘waste’, this method gained popularity through incentivizing the utilisation of normally useless output for profit. Then, through Elif Bilgin’s industrious experiment, the process evolved from using banana pseudo stems to the utilisation of banana peels, a qualitative leap in the plastic. The average tensile strengths of banana peel bioplastics can go over 2kg!
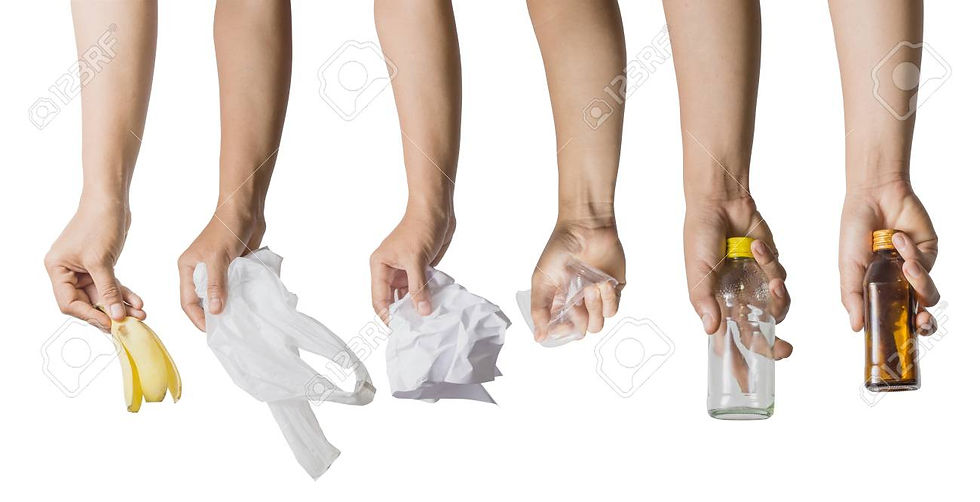
The future of plastic standing with its forebears.
So, how is this done, you may or may not be asking?
Extraction of starch
Step 1: Banana peels are removed using stainless steel knife and converted into small pieces. Then peels are dip in sodium metabisulphite (0.2M) solution for 45 minutes. It is used as antioxidant and preservative. This would increase the biodegradation period of plastic.
Step 2: Banana peels are boiled in distilled water for about 30 minutes.
Step 3: The water is decanted from the beaker and the peels are now left to dry on filter paper for about 30 minutes
Step 4: After the peels are dried, they are placed in a beaker and using a hand blender, the peels are pureed until a uniform paste is formed.

The incomplete phase, a gooey, starchy mess more reminiscent of fecal matter than a plastic baggie.
Production of the plastic
Step 1: 25gm of banana paste is placed in a beaker
Step 2: 3ml of (0.5 N) hydrochloric acid is added to this mixture and stirred using glass rod.
Step 3: 2ml Plasticizer (Glycerol) is added and stirred.
Step 4: 0.5 sodium hydroxide is added according to pH desired, after a desired residence time.
Step 5: The mixture is spread on a ceramic tile and this is put in the oven at 1200 C and is baked.
Step 6: The tile is allowed to cool and the film is scraped off the surface.
Following this, glycerol and plasticizers are added to make it a commercially viable plastic as well as Sodium metabisulphite as an antioxidant to prevent microbial growths.

The brown lump seen in the picture metamorphoses into the modern image of plastic.
So, what reasons do we have to switch over to this fruitier option, besides just the improved quality of plastic? Normal petroleum-based plastic made with the process of polymerisation is non-biodegradable in nature. It takes almost 500 years for them to decompose, and even after that, their residue is toxic and harmful for the environment. But unlike normal plastic, banana peel plastic is made from the banana industry’s agri-waste, and the result is non-toxic, sustainable and biodegradable bioplastic. The biodegradation of bioplastic starts after 3 to 4 months from the date of manufacture. The atmospheric condition also effects on degradation period of bioplastic. Due to its organic nature, the degradation of bio plastic doesn’t produce any harmful gases or pollutants, with the possible exception of minute volumes of carbon dioxide. From both an environmental and an economic perspective, banana-based bioplastics represent the future of the material and maybe we can finally stop paying the customary 20 cents for a plastic bag at 7 eleven.
By Revant Biswas
Comentários